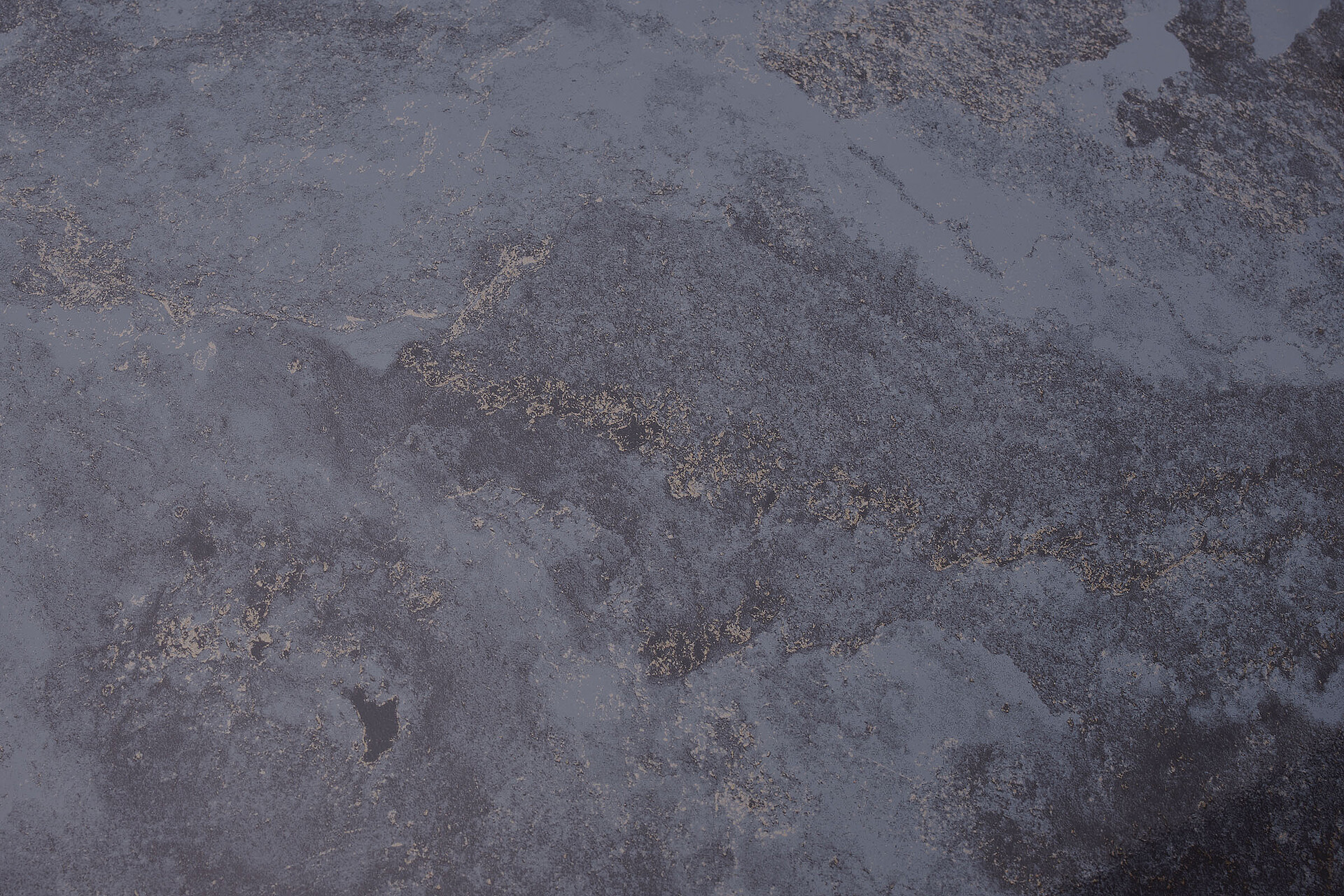
Innovative refrigerator interior:
Sustainable decoration variety for high-end products
Award-winning product series from BSH with LEONHARD KURZ as a supplier
Refrigerators can do much more than just keep food fresh. They have established themselves as technological household fixtures that convey comfort and luxury through high-quality designs.
The challenge
No-Frost technology is now a standard for reducing humidity inside the appliance and protecting food from freezing. This technology requires a refrigerator rear back panel with an integrated airflow system that ensures even air circulation. Decorating this component with individual and trend-setting designs opens up the possibility for manufacturers to offer new high-end products. The production of the decoration should be sustainable and not affect the recyclability of the component.
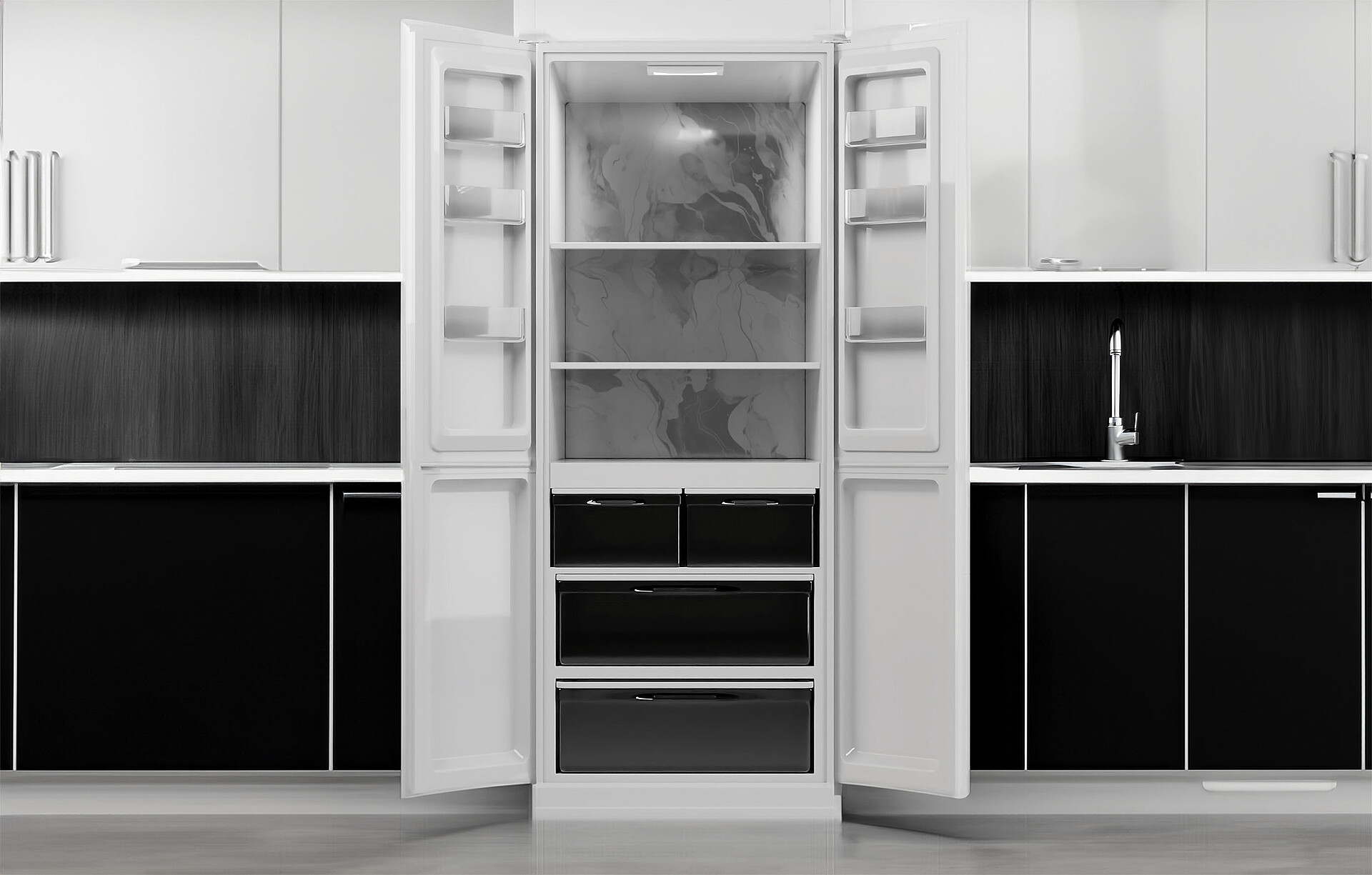
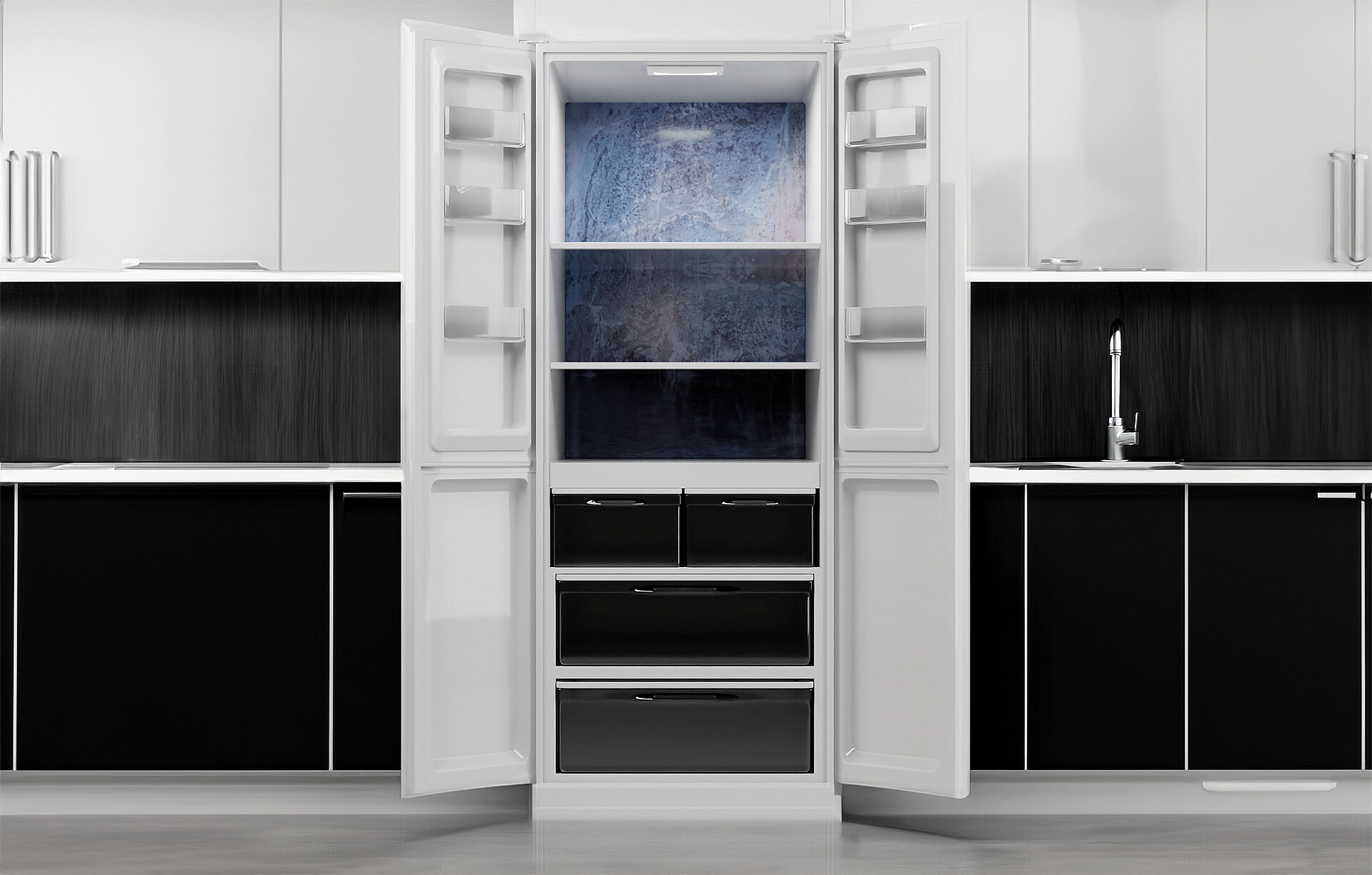
The goal
The BSH Group has been successfully using Hot Stamping decoration for various components in all product lines for decades. Recently, a new design was to be developed for a refrigerator rear panel and implemented using LEONHARD KURZ Hot Stamping technology. To make Hot Stamping possible, the component of the refrigerator rear panel must have a specific geometry.
The current trend for most manufacturers is to cover this component elegantly with real metal - because esthetic and stylish designs upgrade refrigerators to premium products and give manufacturers the option to offer a high-priced product line. Realizing these metal effects on plastic surfaces via Hot Stamping decoration is more sustainable and cheaper than die-cutting and forming thin aluminum plates that are glued to a plastic carrier. With the Hot Stamping process, various metal effects such as brushed stainless steel can be created. The advantage over real metal is maximum design freedom and more diverse possibilities for surface design than with other decoration processes.
The implementation of this project in the form of the BOSCH Series 6 was recognized with an iF Design Award in 2022, one of the most prestigious design prizes in the world.
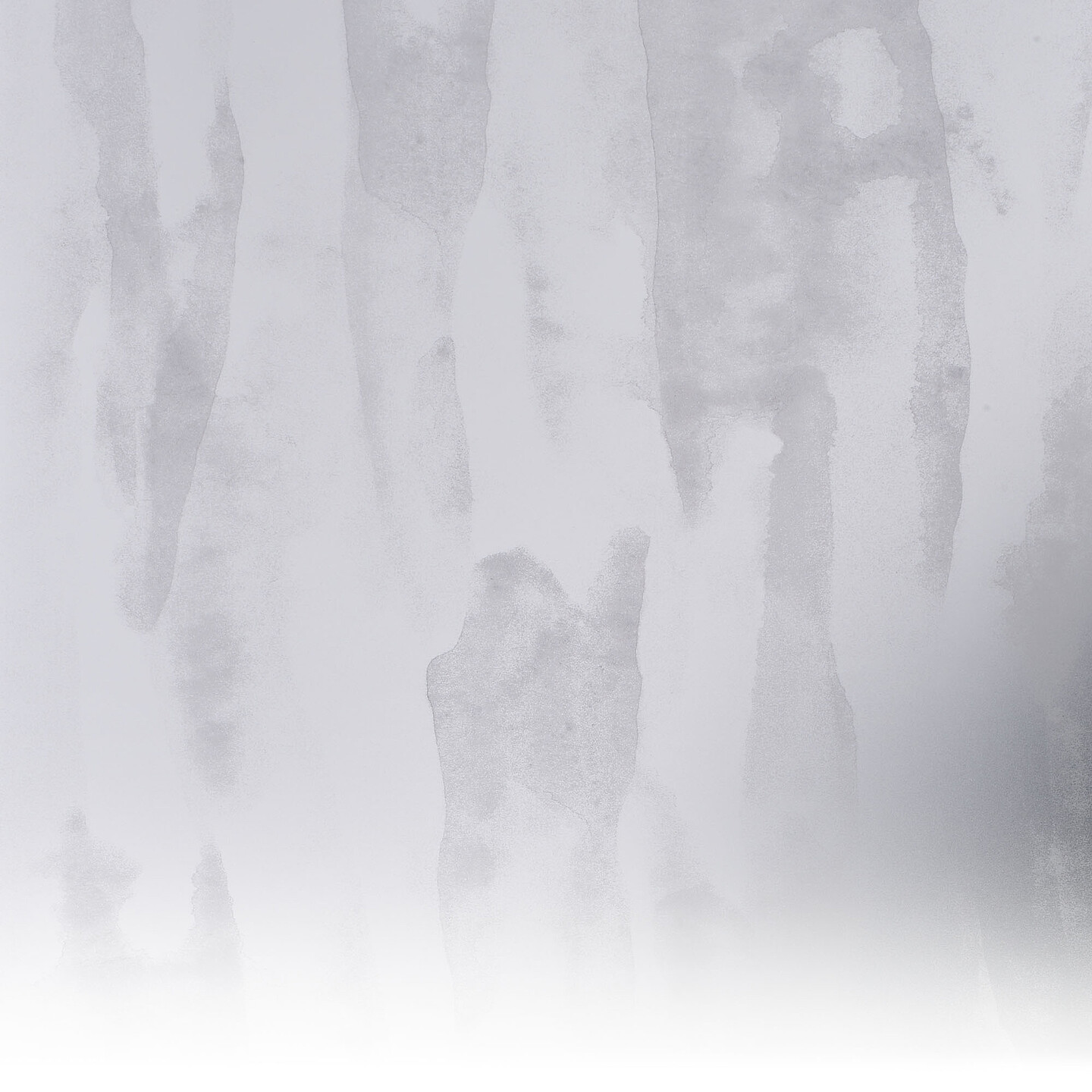
The solution
The Hot Stamping process is ideal for meeting the requirements for decorating refrigerator rear panels because plastic surfaces can be finished with the highest precision. The components are fully or partially decorated in a single step. Sustainable metallizations, for example in a brushed stainless steel look, are just as possible as color gradients, razor-sharp brand stamps, or backlighting.
In this project, the finishing was realized by means of hot and roll-on stamping. The process works in such a way that plastic components that were produced using the injection molding process are placed in a special roll-on stamping machine. The plastic components are placed on a conveyor belt via a workpiece holder, which runs under a heated silicone roller, the embossing wheel. Parallel to the plastic components, Hot Stamping carrier material runs under the embossing wheel, on which the wafer-thin decorative layer is applied. The decorative layer is transferred from the carrier material to the plastic component using heat, pressure, and continuous movement. To this end, the plastic components must meet the geometric requirements for the Hot Stamping process.
This technical procedure is particularly suitable for large surfaces and profiles. Designs can be exchanged in the process within a very short time frame. The decorative layer applied in this way does not affect the recyclability of the component and is inexpensive and efficient to produce.
In the case of the BOSCH Series 6 refrigerator, the decorative strips on the slide-in compartments and shelves are finished along with the rear panel. The Hot Stamping process was also used for the embossed logos.
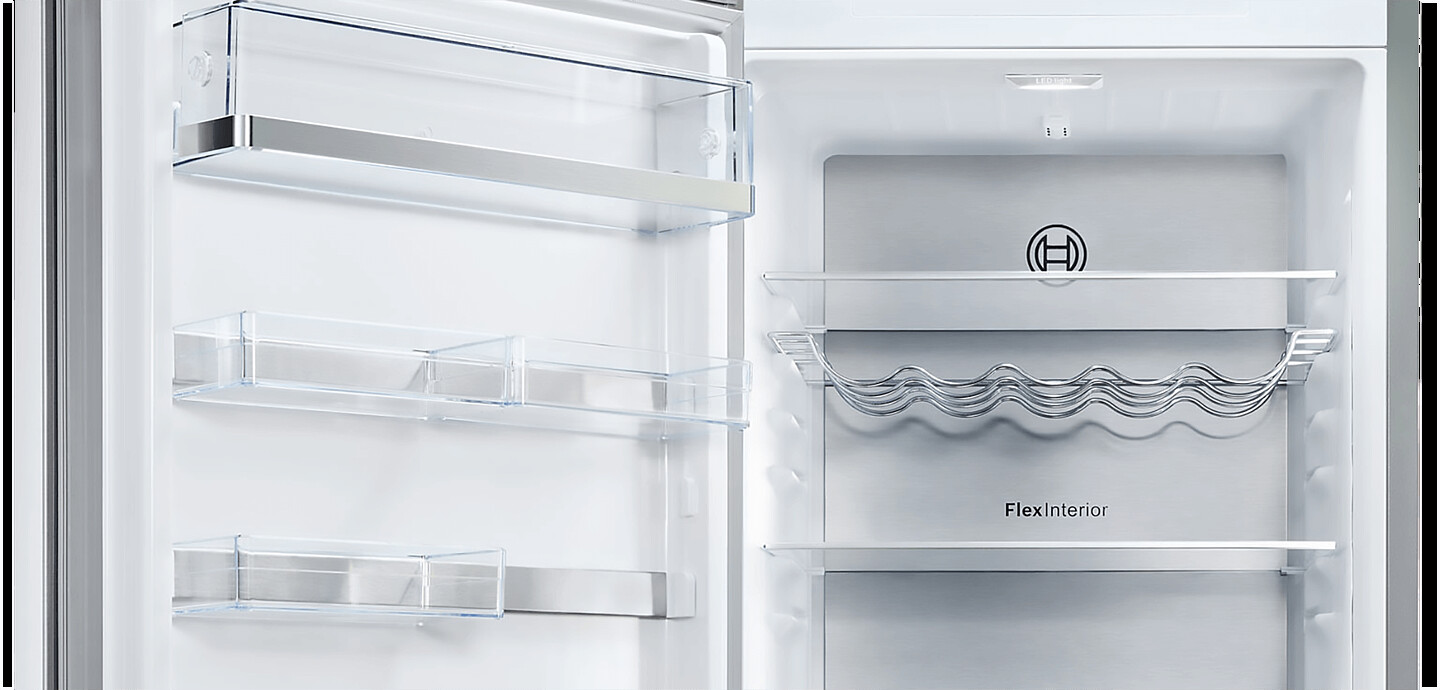
Advantages
Why KURZ has the right solution
- Inexpensive and efficient manufacturing
- Flexible and individual designs such as patterns or backlighting possible
- Designs can be easily swapped during production
- More versatile decoration options than with real metal
- Fully recyclable, no material separation necessary
- Environmentally friendly application process thanks to hot stamping
Conclusion
What makes this joint project so successful is that it responds to huge market demand with a flexible, high-quality, and environmentally friendly solution. Due to maximum design freedom, trends and individual requests can be responded to very quickly. With the decoration of the components for refrigerator interior back panels, KURZ offers a cost-effective manufacturing method for visually outstanding products. The decorative layer does not limit recyclability in any way and can give you a competitive advantage through exclusive designs and premium esthetics.